Livarski vestnik 57 / 2010 št. 1
A. Bührig-Polaczek; M. Mathes; E. Schaberger-Zimmermann
MODERNE ANALIZE METODE ZA PROCESNO KRMILJENJE IN RAZVOJ ULITIH SESTAVNIH DELOV
R. Hanus
NOVA JEKLENA LITINA NAPREDNE KAKOVOSTI Z 9-10% CR JE ROJENA. POROČILO OD IDEJE PREK RAZISKAV DO LIJA POLINDUSTRIJSKIH SESTAVNIH DELOV TER DO TRGOVSKE IZDELAVE TEŽKIH JEKLENIH ULITKOV
J. Stachańczyk, S. Pysz, P. Wieliczko, A. Ościłowski, L. Ościłowski
FILTRIRANJE JEKLENE LITINE - PARAMETRI IN UČINKOVITOST POSTOPKA
A. Bührig-Polaczek; M. Mathes; E. Schaberger-Zimmermann
Moderne analizne metode za procesno krmiljenje in razvoj ulitih sestavnih delov
Povzetek
Mikroskopija, rentgenska analiza, natezni preskusi in meritve dimenzijske točnosti so standardne metode za kontrolo kakovosti procesov litja in ulitih izdelkov. Nadaljnji razvoj teh metod in uporaba novih metod pri vsakdanjem delu v livarni in razvojno-raziskovalnih projektih dajejo nove možnosti za izboljšano optimizacijo procesov in izdelkov. Poleg tega lahko dosežemo dodatno raven kakovosti, če povežemo te metode s simulacijo procesov ulivanja in mikrostrukture.
Nova jeklena litina napredne kakovosti z 9-10% Cr je rojena. Poročilo od ideje prek raziskav do litja polindustrijskih sestavnih delov ter do trgovske izdelave težkih jeklenih ulitkov
Povzetek
Jekleni ulitki iz jekel, odpornih proti lezenju, imajo ključno vlogo v elektrarnah na fosilna goriva za močno obremenjene sestavne dele pri visokotlačnih in srednjetlačnih delih turbin. Notranja in zunanja ohišja, ohišja ventilov, vstopni priključki in kolena so primeri takšnih kritičnih sestavnih delov. Slika 1 kaže prerez parne turbine, kjer lahko najdemo vse take ulite sestavne dele. HP pomeni visokotlačni del, IP srednjetlačni del in LP nizkotlačni del.
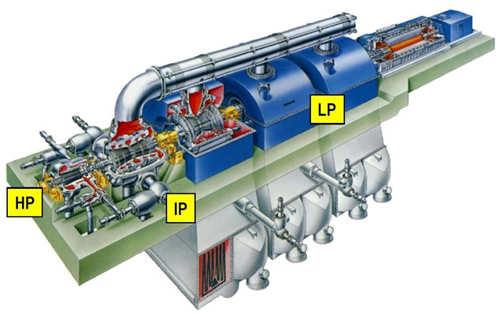
Slika 1: Prerez skozi parno turbino
Najpomembnejša značilnost elektrarne je njen izkoristek, ki v veliki meri vpliva na emisije CO2. Slika 2 kaže odvisnost med emisijami CO2 in izkoristkom. Očitno je, da se emisije CO2 zmanjšajo s povečanjem izkoristka.
Kot posledica stalnega izboljševanja izkoristkov elektrarn in vse strožji standardi za emisije postajajo parametri za paro bolj kritični, lastnosti lezenja materialov pa se morajo stalno izboljševati.
Ni treba omenjati, da se morajo tudi kakovosti jeklene litine prilagajati zahtevnejšim specifikacijam za lastnosti materialov. Sama livarna jekla ne more voditi potrebnega razvoja materialov na ustrezni ravni; zato vsi dobavitelji sestavnih delov elektrarne sodelujejo pri določanju optimalnih kemičnih sestav, pri izdelavi poskusnih talin, preskusih lezenja in preiskavi mikrostruktur, pri preiskavi polindustrijskih sestavnih delov itn.
Članek prikazuje vlogo livarne jekla v okviru programa COST, kjer se razvijajo novi materiali; dodatno opisuje, kako se je nova jeklena litina kakovosti 9-10 % Cr prenesla iz področja raziskav v trgovsko proizvodnjo težkih ulitih sestavnih delov. Prikazane so težave, ki so se pojavile, cikli razvojnega procesa, narejene pa so bile tudi primerjave z običajnimi malolegiranimi jekli.
Ko je bila izbrana najbolj obetajoča zlitina izmed laboratorijskih talin, so bili narejeni preizkusi varjenja – večinoma z elektrodami iz enakega materiala, ki so bile tudi izdelane v okviru COST. Preiskane so bile mikrostrukture, odpornost proti lezenju, mehanske lastnosti in varivost osnovnega materiala ter zvarov. Tudi raziskave toplotne obdelave so potrebne za optimizacijo mehanskih lastnosti.
Na osnovi rezultatov teh analiz so bili uliti polindustrijski sestavni deli in plošče za varilne preizkuse, da bi preverili sposobnost ulivanja in varjenja večjih delov ter da bi po potrebi prilagodili kemično sestavo ter parametre toplotne obdelave ali varjenja.
Vzporedno s preizkusi lezenja po COST so se ta jekla vpeljevala v trgovsko proizvodnjo večjih delov. To je obsegalo iskanje rešitev za procese, ki se nanašajo na težave, kot so dezoksidacija, obnašanje pri strjevanju, toplotna obdelava z dolgimi časi zadrževanja pri temperaturi, varjenje na ulitku, napetosti itn.
V tem času je bilo uspešno izdelanih več kot 200 delov z največjo posamezno maso 60 t. Nadaljnji razvoj v okviru COST 536 bo seveda prinesel nadaljnje izzive – tudi za livarje.
Kot posledica stalnega izboljševanja izkoristkov elektrarn in vse strožji standardi za emisije postajajo parametri za paro bolj kritični, lastnosti lezenja materialov pa se morajo stalno izboljševati.
Ni treba omenjati, da se morajo tudi kakovosti jeklene litine prilagajati zahtevnejšim specifikacijam za lastnosti materialov. Sama livarna jekla ne more voditi potrebnega razvoja materialov na ustrezni ravni; zato vsi dobavitelji sestavnih delov elektrarne sodelujejo pri določanju optimalnih kemičnih sestav, pri izdelavi poskusnih talin, preskusih lezenja in preiskavi mikrostruktur, pri preiskavi polindustrijskih sestavnih delov itn.
Članek prikazuje vlogo livarne jekla v okviru programa COST, kjer se razvijajo novi materiali; dodatno opisuje, kako se je nova jeklena litina kakovosti 9-10 % Cr prenesla iz področja raziskav v trgovsko proizvodnjo težkih ulitih sestavnih delov. Prikazane so težave, ki so se pojavile, cikli razvojnega procesa, narejene pa so bile tudi primerjave z običajnimi malolegiranimi jekli.
Ko je bila izbrana najbolj obetajoča zlitina izmed laboratorijskih talin, so bili narejeni preizkusi varjenja – večinoma z elektrodami iz enakega materiala, ki so bile tudi izdelane v okviru COST. Preiskane so bile mikrostrukture, odpornost proti lezenju, mehanske lastnosti in varivost osnovnega materiala ter zvarov. Tudi raziskave toplotne obdelave so potrebne za optimizacijo mehanskih lastnosti.
Na osnovi rezultatov teh analiz so bili uliti polindustrijski sestavni deli in plošče za varilne preizkuse, da bi preverili sposobnost ulivanja in varjenja večjih delov ter da bi po potrebi prilagodili kemično sestavo ter parametre toplotne obdelave ali varjenja.
Vzporedno s preizkusi lezenja po COST so se ta jekla vpeljevala v trgovsko proizvodnjo večjih delov. To je obsegalo iskanje rešitev za procese, ki se nanašajo na težave, kot so dezoksidacija, obnašanje pri strjevanju, toplotna obdelava z dolgimi časi zadrževanja pri temperaturi, varjenje na ulitku, napetosti itn.
V tem času je bilo uspešno izdelanih več kot 200 delov z največjo posamezno maso 60 t. Nadaljnji razvoj v okviru COST 536 bo seveda prinesel nadaljnje izzive – tudi za livarje.
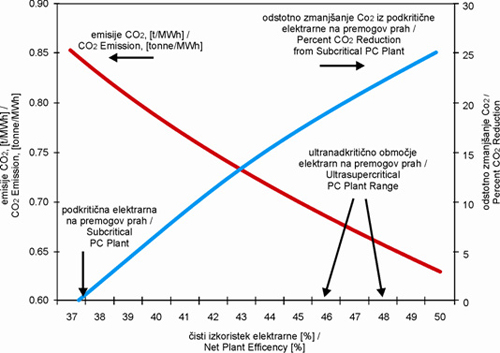
Slika 2: Zmanjšanje emisij CO2 zaradi naprednih tehnologij [2]
J. Stachańczyk, S. Pysz, P. Wieliczko, A. Ościłowski, L. Ościłowski
Filtriranje jeklene litine – parametri in učinkovitost postopka
Povzetek
Članek opisuje področje raziskav in tehnološkega dela, ki se nanaša na filtriranje litega jekla in posebnih zlitin. Prikazani so načini krmiljenja filtriranja s posebnim poudarkom na tehnoloških preizkusih pri uporabi ulitih kovinskih materialov. Pri izbranem postopku ulivanja konzole smo napravili računalniško simulacijo procesa zapolnjevanja votline forme prek ulivnega sistema, v katerem je bil nameščen filter iz penjene keramike. Kot zaključek preizkusov in raziskave je bila izdelana poskusna serija jeklenih ulitkov, ki so bili preizkušeni z namenom oceniti učinkovitost filtrirnega postopka.
V sklepih smo določili nadaljnje usmeritve v razvoju tehnik filtriranja litega jekla in posebnih zlitin s filtri, izdelanimi na Poljskem..
V sklepih smo določili nadaljnje usmeritve v razvoju tehnik filtriranja litega jekla in posebnih zlitin s filtri, izdelanimi na Poljskem..